10th EASN Virtual International Conference
LABOR Technical Workshop
The LABOR Technical Workshop was held as a virtual event of the 10th EASN International Conference on Innovation in Aviation & Space to the Satisfaction of the European Citizens on September 3rd 2020 at 14:30 CEST. The workshop consisted of 6 oral presentations of selected contributions and a panel discussion.

FUNDING
This workshop has received funding from the Clean Sky’s Horizon 2020 research and innovation program under grant agreement N° 785419

ORGANIZERS
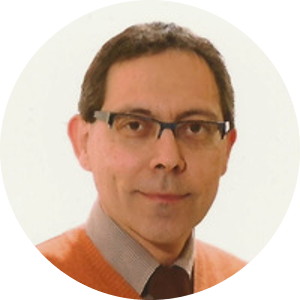
Prof. Ciro Natale
UNIVERSITà DEGLI STUDI DELLA CAMPANIA LUIGI VANVITELLI

OBJECTIVE
The LABOR Technical Workshop is aimed at presenting some of the most recent technological advances in manufacturing, assembly and inspection of aerostructures. The workshop gathers contributions from four projects funded within the Green Regional Aircraft ITD of the Clean Sky JTU, working on different steps of the manufacturing and assembly of the hybrid aircraft fuselage. The workshop will pay particular attention to the industrial experience and challenges, discussing applicable solutions to save major equipment costs, to reduce the whole production time, to improve efficiency rates and flexibility, maintaining high quality standards of the assembly and manufacturing. A final panel discussion will take place to involve all stakeholders of the design, manufacturing and assembly processes of the regional aircraft of the future.

PROGRAM
LABOR TECHNICAL WORKSHOP
1st presentation
Clean Sky 2 - REG IADP Overview and links with AIR ITD
Vittorio Ascione, Vito Perrupato, Rossella Valiante
Leonardo
A presentation by Leonardo Aircraft during the 10th EASN Conference will give a brief overview of the Regional IADP (REG IADP) and its main links with the Airframe ITD (AIR ITD) in the frame of the Clean Sky 2 Programme.
Innovation in manufacturing and assembly automations matured in the AIR ITD with contributions of dedicated Projects selected through the CS2 Call for Proposals instrument finds a direct application in achieving one of the major REG IADP deliveries: composite fuselage full-scale integrated on-ground demonstrator.
Such presentation includes the following topics:
- High Level Plan for Clean Sky 2,
- The REG Team,
- Work breakdown Structure,
- Interfaces with other SPDs,
- Major Demonstrators,
- Automation from AIR ITD to REG IADP.
2nd presentation
New concepts for a robotized cell for the assembly and control of composite fuselage panel components
MATTEO Nisi, DANIELE Massa, ANDREA Bruni, CRISTINA Cristalli
Research for Innovation, Loccioni - Via Fiume 16, Angeli di Rosora (AN), Italy
According to the Global Market Forecast 2018-2037, there is a strong need to increase productivity in the aviation industry and, to this end, all manufacturers are investing in order to reduce the production costs and increase their efficiency in particular in the construction processes of aeronautical components and their assemblies. Robotics is a key technology, but current commercial robotic systems for assembling aeronautical structures are usually using automatic systems with large payloads, large dimensions and large investments. The LABOR project aims to overcome these obstacles in the automation of some critical assembly operations, proposing a new approach. The proposed technological strategy consists in the adoption of two medium size robots which, based on real time measurements, adapt to the environment in which they operate and to the operations to be performed, integrating quality control systems for the assembled components. The cell is equipped with a dedicated vision system that is adopted to guide the processing in a self-adaptive way (thanks to the real-time scanning of the components) and to check the quality of the components, in order to guarantee a high standard of the process.
The operations that the cell can perform automatically are as follows: referencing of the robot working area on the basis of the recognition of geometric features of the parts to be coupled (edges, holes, etc.); “one shot” drilling and countersinking operations; automatic control of the holes; installation and sealing of the connection units, plus their correct installation control including the “flushness”; reporting. Furthermore, it is possible to have activities in co-working with operators such as insertion and removal of temporary connecting parts, application of sealant by interposition, removal of metal burrs on the edge of the holes.
The project started in March 2018 as part of the European Clean Sky 2 research program and now, after the competition of the assembly of the cell, the tests on real panels started. The installation of the LABOR cell and the demonstrations are scheduled at the Leonardo S.p.A. site of Pomigliano.
3rd presentation
Collaborative robotized assembly of composite fuselage panels
GAETANO LETTERA, CIRO NATALE
UNIVERSITà DEGLI STUDI DELLA CAMPANIA LUIGI VANVITELLI
Human-robot collaboration (HRC) represents one of the major areas of exploration for the aerospace manufacturing sector of the future. Even though robots can be good for a number of assembly operations, e.g., drilling, fastening, inspection, intervention of the human operator is required in several phases of the assembly process, e.g., dismantling for deburring of hybrid metal-composite structures. Therefore, suitable safety measures have been taken to prevent injury of the workers sharing their workspace with robots. Besides standard safety procedures and countermeasures established by the current regulations as ISO 10218-1/2 and ISO/TS 15066, a novel workspace monitoring approach based on multimodal sensing has been developed for the LABOR workcell, with the aim to maximize the system productivity and preserve operator safety at the same time. Achieving such conflicting objectives is challenging: on one hand, a perception system is needed for monitoring human presence reliably, on the other hand, suitable control algorithms are needed to be devised to select the proper robot behaviour for keeping a high level of productivity during the collaborative activity, i.e., reducing at a minimum the number of robots stops during the assembly process.
4th presentation
Robot deployed Laser-Ultrasonic NDT system for inspection of large aircraft structures
Vicki James1, Dave Carswell1, J Riise1, P. Ian Nicholson1, Norbert Graf2, Norbert Huber3, Martin Gärtner3, Bernhard Reitinger3, Edgar Scherleitner3, Peter Burgholzer3, Jon Phipps4, Dave Burns4, Ciro Incarnato5
1TWI Technology Centre Wales, UK - 2InnoLas Laser GmbH, Germany - 3RECENDT GmbH, Austria - 4KUKA Systems UK Ltd, UK - 5Leonardo S.p.A.
The mandatory Non-Destructive Testing (NDT) by the aerospace industry for both present and future generation hybrid aircraft using thick composite structures poses many challenges for traditional inspection techniques. Laser Ultrasonic testing (LUT) deployed by a robot for inspection of modern aerospace composite components shows good promise. It is a non-contact method offering the possibility of fast scan times without the need for couplant.
This paper presents the latest work-in-progress for the design and development of the system developed by the ACCURATe consortium. ACCURATe is an ongoing H2020 CLEANSKY 2 part funded project to develop a laser ultrasound based NDT system prototype for fast and contactless testing of large carbon fiber reinforced polymer (CFRP) aircraft structures.
The approach is based on a non-contact laser generated and detected pulsed ultrasound technique with delivery of both the laser ultrasound excitation and detection pulses through flexible optical fibres. The backscattered light from the lasers is also collected into a fibre. The measurement head, which contains the two beam outputs and the light collection optics is raster scanned over the surface by a 6-axis robot arm. The excitation and detection lasers are based on diode pumped Nd: YAG lasers, which enable a low profile casing with low weight and very long lifetime with little maintenance and high nominal scanning speed of 400Hz. For the demodulation of the ultrasonic waves, a two wave mixing interferometer (B-TWM) is used. The robot arm is mounted on a rail and raster scans the laser head system over the part surface, and moves in increments along the track to inspect the whole component.
The system has recently been used to scan a reference panel, specially created for the project. This panel has 125 artificial flaws, which were created by insertion of alien materials into the layers of the FRP before infusion and cure of the panel. The panel also has regions where viscoelastic material is present, and regions with differences in thicknesses and composition. The latest test results are presented.
5th presentation
TOD – Thermoplastics on Doors: Development of full scale innovative composites doors, surrounds and sub-structure for Regional Aircraft Fuselage barrel on-ground demonstrators
Sampethai Sofia, Antonio Miraglia, Francesca Felline, Ciro Rocco, Alesandro Ceresa, Umberto Raganato, Miguel Zavala, Bertrand Flipo, Georgios Liaptsis, Jonathan Riise, Xiaofei Cui, Minghui Wu
MSc, BSc, CEng MWeldI - Adhesives, Composites and Sealants, Polymer and Composite Technologies Group
Thermoplastic composites can reduce cost and save weight in airplane structures. Currently on the market there is no thermoplastic door available for commercial aircraft. The overall goal of TOD project is to demonstrate and validate the manufacturing process of thermoplastic door components, induction welding assembly process, additive manufacturing and metallic parts of door mechanism, metallic and thermoset parts of surrounding structure of the passenger and service door of an aircraft The impact associated with the activities performed in TOD project is related with the following:
- Use of thermoplastic materials and the development of out-of-autoclave manufacturing processes, which are drivers of manufacturing cost reduction and of manufacturing rate increase. These technologies are projected to 75% energy savings over standard autoclave processing
- Minimum 15% weight reduction on structural components as doors. Recent thermoplastic composite studies already demonstrated the substantial weight reduction that can be obtained by combining automated production processes and thermoplastic materials. Specifically, in aircraft related components, an approximate 10% weight reduction of the torsion box of the tail has already been achieved using thermoplastic composites.
- Reduction of Recurrent Cost considering the conception of an adaptive and smart manufacturing equipment to: 1. Increase production flexibility; 2. Decrease the full line tools cost
- Reduction of waste and scrap by 10% by working directly at the defects root cause with a multidisciplinary approach thru the sensors for in-line monitoring directly connected to the manufacturing equipment
- Significant eco-impact reduction through the component’s and aircraft’s life-cycle: the reduction of energy usage during manufacturing of thermoplastics, combined with the light-weighted parts will contribute to the reduction of CO2 emissions during both product manufacture and operation
- TOD addresses a key issue of extensive use of out-of- autoclave composite with aerospace relevance. The R&D work will generate new scientific knowledge as well as new technologies, and thus strengthen the European positions in this field.
TOD project has received funding from the Clean Sky 2 Joint Undertaking under the European Union’s Horizon 2020 research and innovation programme under grant agreement number 821192.
6th presentation
SPARE project – improvement of continuous compression moulding process for the production of thermoplastic composite beams
Riccardo Angiuli1, Federica Dell’Anno2, Leonardo Cosma1, Umberto Raganato1, Alessandra Passaro1
1CETMA Technologies Design and Materials European Research Centre, Italy - 2OMI Officine Meccaniche Irpine, Italy
In recent years, thermoplastic matrix composites have seen an increasing interest from the research and development sector due to the versatility of use and the wide potential in sectors such as automotive, aeronautics and transport.
Furthermore, the thermoplastic matrix allows the use of simpler, faster and automatable production cycles and joining systems. As part of the SPARE project, the continuous compression moulding process (CCM) was upgraded using as numerical simulation, monitoring via infrared thermography and induction welding.
Thanks to these innovations, the CCM process can ensure savings in terms of production costs, reduction of waste and a higher level of automation, the proposed work will illustrate the activities carried out during the project. The numerical simulation was used to analyze the heating process and verify its uniformity in order to identify the best configuration to obtain uniform heating, infrared thermography, on the other hand, was used to continuously monitor the temperate of the laminate at the entrance and exit of the compaction zone and to measure the process temperature and the degree of uniformity.
Finally, at the end of the production process, a tool was developed for the induction welding of the laminates for the construction of complex beams with a T or H cross section.